It's important when you're choosing your diamond burs that you consider how they were created. We're open with our diamond manufacturing process and want to make sure you're informed on how our diamond burs go from a blank all the way to your office.
Diamond Blank is Produced
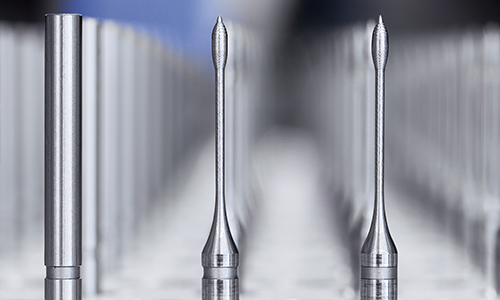
The first step of our diamond manufacturing process is creating the blank on a CNC Turning Lathe. It has no diamond particles yet.
Ultrasonic Cleaning
Next, the blanks go through their first of many ultrasonic cleanings. This helps prepare it for future steps by ensuring that all foreign material is removed.
Isolation
The blanks are isolated / covered in areas where there should be no diamond particles.
Coating
The blanks are dipped into a chemical bath called Galvanic Bonding, creating a bonding layer that the diamond particles will adhere to. Next, the blanks are dipped into the diamond bath.
Color Coding
The diamond burs are color coded according to their grit. For more information on our color-coding system,
check out our guide.
Optional Shank Coating
If required, some of our diamond burs will be dipped in a bath to change the color of the shank.
Final Ultrasonic Cleaning
The diamond burs are cleaned one last time to ensure that all debris has been removed.
Quality Check
Every production batch will be checked according to our high-quality standards.
Packaging
Our burs are packed under cleanroom conditions. Afterwards they will be sterilized to be ready to use immediately.
These steps assure that the diamond bur is a perfectly concentric cutting instrument for optimal operation every time.